People
Dr. Shigetaka Tomiya, Sony’s Corporate Distinguished Engineer and Japan Society of Applied Physics Fellow, Speaks about the Future of Materials and Devices
Dec 7, 2021
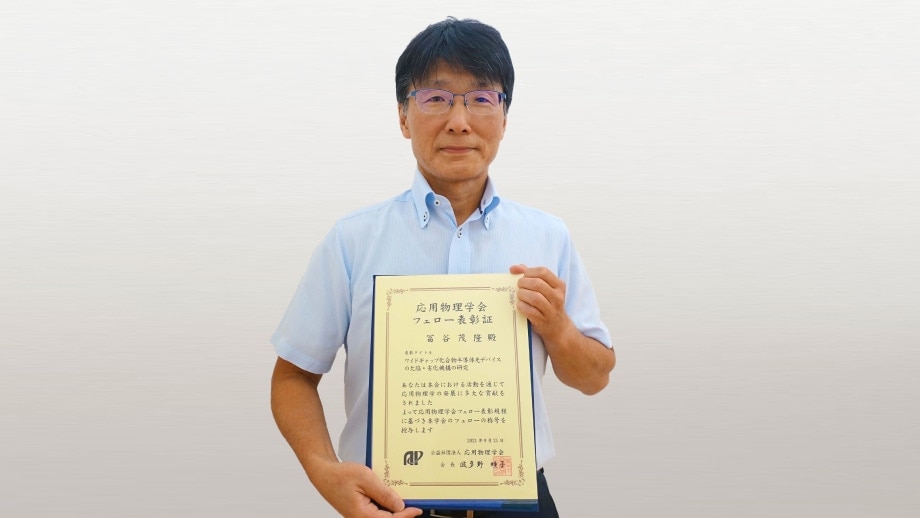
Sony’s Corporate Distinguished Engineer Dr. Shigetaka Tomiya has been honored with the 15th JSAP Fellow Award by the Japan Society of Applied Physics (JSAP). JSAP Fellows are individuals who have made remarkable contributions to the progress of applied physics. We spoke to Tomiya, who has a wealth of experience at Sony Group in materials analysis and device development, and is actively engaged in various efforts in industry and academia outside Sony, about his background, research, and the future of the materials and device fields.
Profile
-
Shigetaka Tomiya, Ph.D.
Distinguished Engineer
Sony Group Corporation
Building a career while pursuing the heart of the matter
In university I majored in theoretical physics, studying condensed matter theory and statistical physics, while also engaging in research on molecular dynamics and quantum dots. I was so interested in space during high school that I wanted to work at NASA in the future, and I thought that physics was the key to understanding the heart of the matter. After entering the university, however, my interest shifted to condensed matter physics. Seeing the latest collaborative efforts by JAXA and Sony, I have to admit I feel very envious. I have always been interested in seeking out the heart of the matter, so I think that part of my nature has led to my current career.
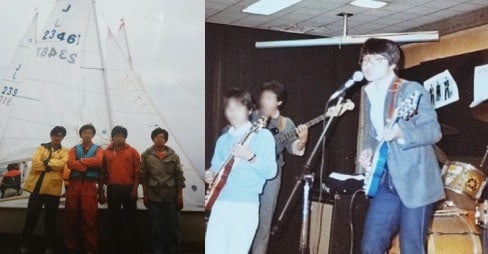
During his university days, in addition to research, Tomiya was in the yachting club and participated in school festivals
The reason I decided to join Sony was because of a special lecture given by the late Dr. Makoto Kikuchi, head of the Research Center at the time, at Keio University where I was studying. During the lecture, Dr. Kikuchi talked about his activities at Sony and how he interacted with Nobel Prize winners such as William Shockley and John Bardeen during research and development in semiconductors, his field of specialty. The more I learned about his story, the stronger my desire to work at Sony became. My ambition to create valuable devices that would go beyond existing semiconductor devices — things the world had never seen — and to discover new phenomena and utilize them to contribute to the world grew stronger, and I believed that Sony was the best place to accomplish these goals.
Later, my wish came true. I joined Sony in 1988 and was assigned to the Research Center where Dr. Kikuchi worked. At that time, I was engaged in compound semiconductor material and device analysis using transmission electron microscopy. I analyzed materials such as GaInP (gallium indium phosphide), used in red laser diodes for DVD recorders, GaSb/InAs (gallium antimonide/indium arsenide) for bipolar transistors and ZnSe (zinc selenide) for aiming shorter wavelength laser diodes. Instead of being limited to compound semiconductors, I was also in charge of analyzing cathode materials for lithium-ion batteries.
At that time, the company was actively promoting research and development overseas, so I signed up for an overseas study program, which led me to study for a year and a half as a researcher at the Materials department of University of California, Santa Barbara. There, I was engaged in fabricating semiconductor quantum wires and quantum dot structures and characterizing their optical properties microstructures. During the course of my work, I engaged in joint research and discussions with various others in fields such as Electrical & Computer Engineering (ECE), Physics, and Chemistry department. It was thanks to that environment that I was able to interact with those professors, who would later go on to win Nobel Prizes in Physics and Chemistry. I was truly blessed to enjoy such a time and have the life of a researcher, and felt I had found the future I had envisioned as a student.
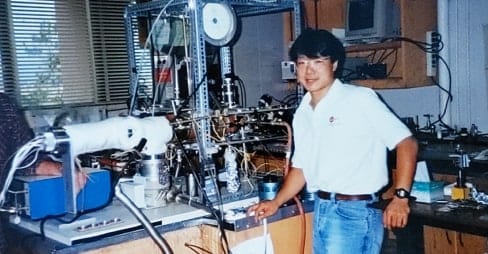
In front of a quantum dot fabrication apparatus at UC Santa Barbara
After returning to Japan, I worked at the then-Materials Laboratories where I focused on research and development of a blue-green laser diode using ZnSe materials, contributing to the development of a ZnSe laser diode with the longest lifetime in the world.* Unfortunately, that ZnSe laser diode was never commercialized, but I was also able to focus on the research and development of a laser diode using GaN (gallium nitride), the material that was widely recognized by the 2014 Nobel Prize in Physics. We succeed to develop the GaN-based ultra-high-output pure-blue laser diodes used for the 2005 large-format projector displayed at the Sony booth during Expo 2005 in Aichi Prefecture, Japan. Although crystal defects were a critical issue during the course of development, I succeeded to find the cause and work out a solution, resulting in being honored as a Sony Most Valuable Professional (currently, the Sony Outstanding Engineer Award). At the same time, I also engaged in developing a triple wavelength laser diode for the PlayStation® 3, which proved very difficult to mass-produce at the initial period. Traveling repeatedly between Sony Shiroishi Semiconductor (currently Sony Semiconductor Manufacturing Corporation [SCK]), a production site in Miyagi Prefecture, and the R&D site at the Atsugi Technology Center (Atsugi TEC) in Kanagawa Prefecture, we thoroughly investigated the problems, finally managing to solve the issue and achieve mass production. For several months, there were times when I was unable to take a break, but looking back on it now, it was a time full of memories and good hardships.
In 2010, I was transferred to SCK in Miyagi, where I was involved in various tasks pertaining to quality and reliability. After the Great East Japan Earthquake in 2011, I was involved in the restoration of the factory. Later, after I returned from SCK, I was transferred to the display-light-source development department at Atsugi TEC, where I was in charge of developing GaN-based green laser diodes and improving their reliability. Recently at the R&D Center, I’ve worked in management, and as a DE I’ve been engaged in material analysis and simulations for various devices such as image sensors including organic ones, and optical semiconductor devices. At the same time, I am also involved in research and development into materials informatics, which I will touch on later, as a way to accelerate the development process of materials and devices, which tends to take quite a long time.
※As of 1997
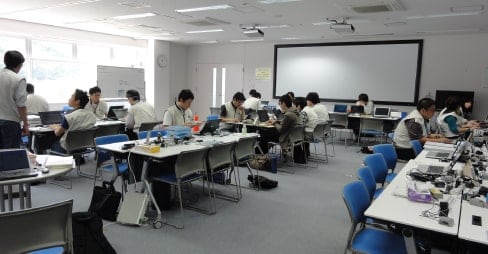
Because the office was unavailable due to damage from the Great East Japan Earthquake, the whole team worked in the meeting room until the restoration was complete
Learning from the hardships of materials R&D, to take on the challenge of streamlining work through analysis
During the development of a ZnSe-based blue-green laser diode at the Materials Laboratory, we achieved the world’s longest lifetime of over 100 hours, and I identified the causes and mechanisms behind defects and failures. Later on, however, we were unable to extend the lifetime as expected, making it impossible to use as a product, so unfortunately we were forced to give up on ZnSe materials. However, at just about the same time, I shifted to research on a blue GaN laser diode, establishing the world’s first practical use GaN board fabrication technology for laser application, which was then patented. Later on, we succeeded in developing a GaN-based laser diode with an extending lifetime, which was then commercialized.
This GaN-based laser diode is still used in various Sony products, such as Blu-ray disc recorder and PlayStation® pickups.
I was awarded the title of Fellow for study on defects and degradation mechanisms in wide-bandgap compound semiconductor optical devices such as ZnSe-based and GaN-based materials.
Additionally, I believe that it was taken into account that I have been promoting collaboration on materials informatics with communities including academia outside the company to address the issue that material and device research takes a long time.
Harnessing the “four sciences” in materials informatics
Materials informatics is an approach that allows AI to learn from existing experiment and simulation data to infer the cause from the results to arrive and derive new materials with the desired physical properties from the data. Utilizing AI is a vital part of the process, but it is also said to be an efficient way to search for materials with specific function by fully utilizing the four sciences: experimental science, theoretical science, computational science, and data-driven science.
Conventionally, experimental science was used to reveal patterns and laws in data and to formulate hypotheses, or theoretical and computational sciences were used to make predictions. On the other hand, materials informatics repeats the cycle of discovering the law of pattern in data, formulating a hypothesis, making predictions, and creating data. Data is the critical element in the process, and growing emphasis is placed on how AI is used to uncover patterns in data in recent years. When speaking of materials informatics, people often think of AI, but as mentioned above, AI is not the be-all-end-all component; rather, it goes without saying that skillful use of AI is the key.
The precedent for such a practice of using data in scientific methodology can be found in bioinformatics, which was used to discover the DNA base sequence, and in cheminformatics used for drug development. Materials informatics aims to apply these kinds of methodology while utilizing AI to organic and inorganic materials, as well.
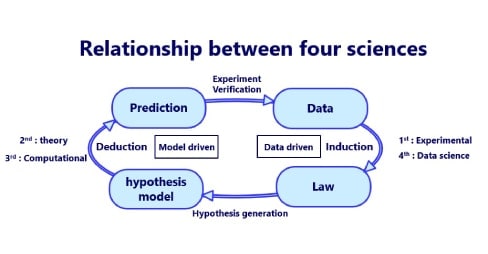
As seen in examples such as Teflon and lithium-ion batteries, the research and development timeline for materials and devices tends to be quite long. This is true at Sony, as well, where research into fields such as semiconductor lasers and image sensors began in the 1970s but has only recently become a specialty at Sony. Materials informatics is a method that is used to streamline and shorten such long research and development processes as much as possible. Also, streamlined and shortened research and development periods are expected to reduce research expenses, leading to environmentally friendly research and development.
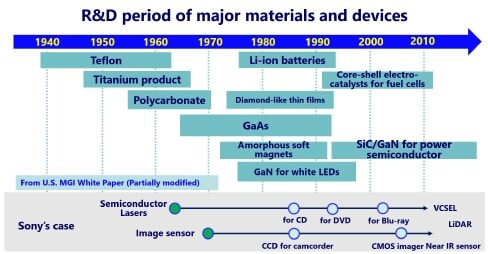
At Sony, we do our best to utilize the four sciences, while also leveraging the knowledge and resources of the R&D center in such areas as computational simulations, data science, high throughput experiments (a new, high-speed experimentation method), and materials analysis.
The secret behind powerful technology is human connection
In 2013, I took the lead in establishing the Materials Analysis Network as a cross-Sony group activities for engineers engaged in materials analysis and reliability in R&D Center, business units, and production sites. The trigger for this network was the idea of raising the bar for our technical capabilities by skillfully collaborating and utilizing in-house assets and resources. I believed that connections between people were vital, and I sought to strengthen them.
At Sony Group, there are many people involved in materials and device characterization and analysis, not only in the R&D Center but also in various businesses units and production sites. Before the network was established, there was no system or framework for collaboration between engineers in different organizations, so it began with volunteers. I personally had experience in being assigned to different offices and sites in Japan, so I realized just how important such initiatives were. Working in the R&D division, we can develop new things based on our unique viewpoint, while serving at business units and production sites can come up with our new ideas and needs, so I believed that collaboration could help our materials and device analysis work more effectively. There were many tried and trusted team members at the business units and production sites, so launching the network went smoothly. Later, cross-functional activities began at the in-house Technology Strategy Committee, further strengthening the network.
We also hold an in-house material analysis forum every year with the hope that it will create new ideas (held online last year and this year). This provides an opportunity to meet and communicate with material analysis network members across Sony Group that we usually do not have the chance to see, making it a good venue for sharing knowledge and formulating new ideas.
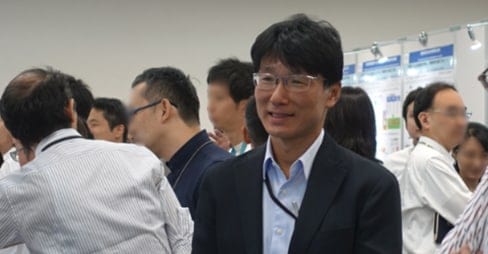
At a previous material analysis network forum
Using materials and devices to help solve social issues
Because I myself decided to join Sony due to the influence of a lecturer back in the university days, it is with great fondness that I work as a Specially Appointed Professor at the Tokyo Institute of Technology. Through my work at the laboratory and communication during lectures, I explain what it is like to join a company and engage in research and development and discuss the excitement of making products and contributing to society, all based on my own personal experience. Students have become interested in Sony as a result of the laboratory work and discussions in lectures, and some of them have even come to work with us.
At the Research Center for the Earth Inclusive Sensing of Tokyo Institute of Technology, where I work, there are various efforts in addition to materials and devices. I am also working on the research of materials and devices that can convert heat into electricity. This subject is an important one for addressing energy issues.
Consideration of the global environment is an essential part in thinking of future technologies, so I always make sure to communicate the importance of this and trends in research in this area. Thankfully, I believe that students keep this viewpoint in mind in their research and studies.
I personally have a strong desire to use currently available technology to help solve social issues — for example, thermoelectric devices and technology for ultra-low-power consumption to address energy issues. I am also active as a DE at Sony, where I work with other DEs not only on technical issues, but also discuss with them how various social issues can be solved, from diverse perspectives.
Looking back on the social changes and innovations during my lifetime, it is clear that materials and devices such as semiconductors have been major factors. However, as the source of added value shifts from tangible to intangible things, there is more and more importance being attached to virtual things instead of real things. Looking across Sony’s diverse business domains today, the role that innovation in the areas of materials and devices plays within the overall group may be not as important as it once was. However, in the real spaces where people and things work, there will always be a touchpoint in the form of materials. In virtual spaces such as the metaverse, as well, it still remains the fact that materials and devices are essential and significant as a human touchpoint.
Materials innovation will be necessary in the future for bolstering cutting-edge technology domains such as AI, biotechnology, and quantum computing, as well as for achieving the SDGs and solving social issues, such as overcoming resource and environmental limitations and achieving a safe, secure society with healthy longevity. I believe that, going forward, we need to think of materials and devices from a group-wide perspective — looking for the ones that can leverage Sony Group strengths in order to solve social issues.