Cutting Edge
イメージセンサーという「小宇宙」を創造する者たちの視座
2019年4月10日
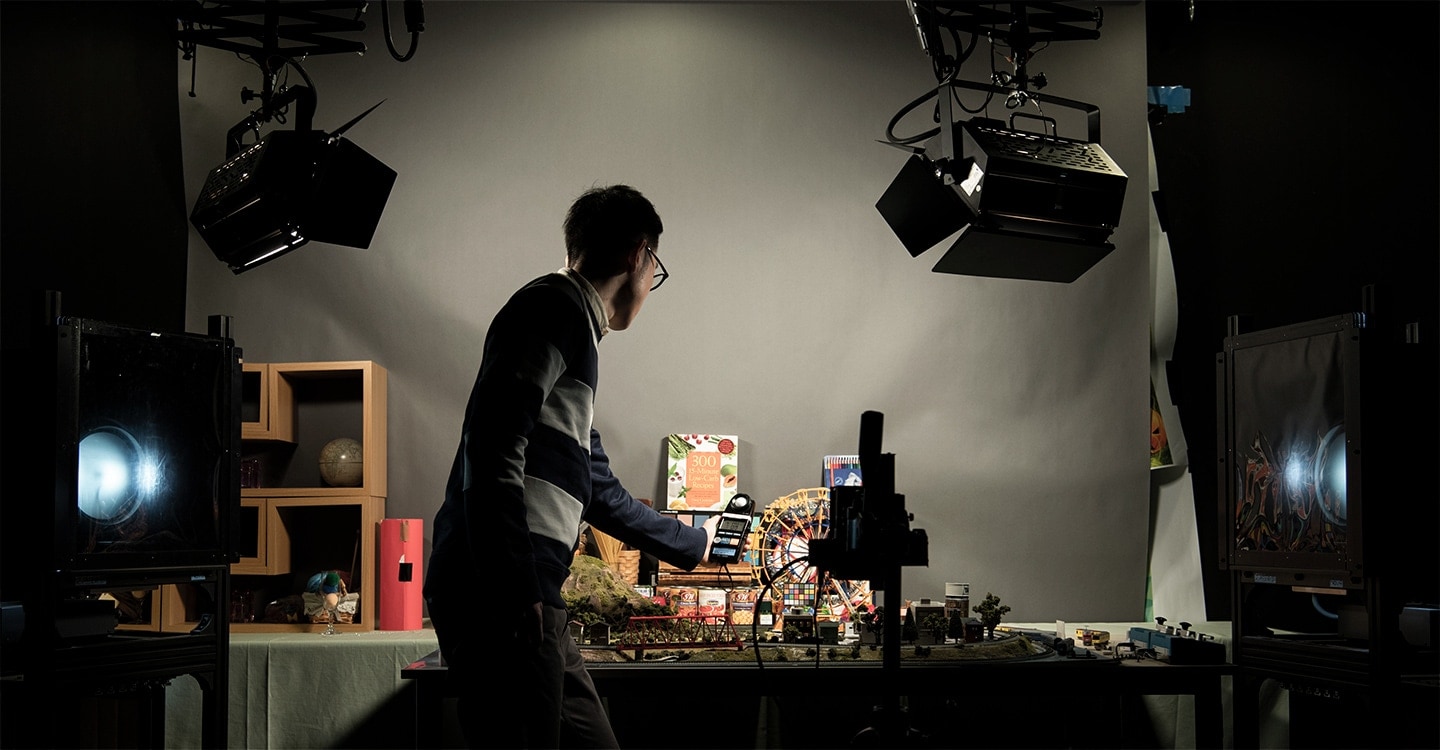
ソニーが、スマートフォン向け積層型CMOSイメージセンサー『IMX586』の商品化にこぎつけたのは2018年7月のこと。0.8μm(世界初※)という微細な画素サイズによって、業界最多となる有効4800万画素を実現し、撮像素子のさらなる高画質化を達成した『IMX586』の開発過程では、いかなる苦悩やブレイクスルーがあったのだろうか。画素設計、画像処理アルゴリズム、デバイス。それぞれの担当者に訊いた。
※ イメージセンサーとして。ソニー調べ。(2018年7月23日広報発表時)
プロフィール
-
中溝 正彦
ソニーセミコンダクタ
ソリューションズ株式会社
モバイル&センシング
システム事業部 -
藤田 和英
ソニーセミコンダクタ
ソリューションズ株式会社
モバイル&センシング
システム事業部 -
渡辺 朋幸
ソニーセミコンダクタ
マニュファクチャリング
株式会社
MIS製品部門
画素設計
小型化のトレンドはまだ続く?
──最初に、「イメージセンサーにおける画素の役割」について教えていただけますか?
中溝:レンズから入ってきた光を電気信号へと変換する、目に見える実世界から電気的な世界への入り口に当たるのが画素です。画素で変換された電気信号が、アナログ回路やデジタル回路を通り、画作りに進んでいきます。逆にいうと、その入り口の画素の段階で入ってしまったノイズ等を取り除いたり、拾いきれなかった信号を復元したりすることは、基本的に難しい。画作りの根本は画素の信号から始まるので、「そこにないもの」は作ることができないんです。
──なるほど。では、今回の『IMX586』はどのような背景から開発がスタートしたのでしょうか?
中溝:イメージセンサーの面積が同じだとすると、画素が小さい方が当然、より多くの画素を並べられるので、画像の解像度が上がります。ここ最近はスマートフォンのカメラがますます高性能化しているので、その要望に応えるためにも、画素の小型化に各社が力を注いでいる状況です。競争力という意味でも、他社に先んじて微細な画素を開発する必要がありました。
IMX586は、サイズが1/2インチ(対角8.0mm)でありながら0.8μmという画素サイズを実現できたことで、有効4800万画素という解像度を実現することができました。

──0.8μmが出るまでの、最小の画素サイズは?
中溝:0.9μmで、その前は1.0μmでした。このたった0.1μmの小型化が非常に大変なんです。小型化はこれまでの流れからも予想していて、お客様から具体的な要望が来る前に内部で開発を始め、商品化が決まったらそれに向けて一気に開発を加速していく、という感じでした。ただ、小型化のトレンドは、そろそろ転換期に入りつつあります。単純に小さくするだけでは、いつかは限界が来ますし、小型化によるトレードオフもあるんです。
さらなる性能向上の鍵は「全体最適化」にある
──小型化にもメリットとデメリットがあるんですね。
中溝:はい。小型化のデメリットは感度が下がっていくことです。感度が下がらないように技術開発していくのですが、そろそろ画素の小型化とは違う方向にも価値軸を作っていかないといけないところに来ています。そのために、どのように新しい価値を作っていくかを、いろいろと議論しています。センシングの機能を取り込むとか、高い解像度だけではなく画素や回路などトータルで一番キレイな画像を作るにはどうしたらいいか、といった視点で考えています。ほかのチームとコラボレーションしながら、これまでより特性がよくなるポイントを探し当て、新しい性能向上の方法を探っているところです。
──今回のIMX586の開発にあたって、全体最適化によって課題をクリアしたケースはありましたか?
中溝:画素サイズの小型化に挑む時は、プロトタイプを作って評価をします。これまでは、評価結果を画素設計の知見や方針にフィードバックして終わりだったのですが、今回は、プロトタイプの段階で、信号処理やアナログ回路、デジタル回路の担当者と協議を重ね、のちに出てくるであろう課題の抽出と対策を事前に検討し合いました。
特に信号処理のハードウェアは、設計初期段階で仕様が決まってしまい、一度回路ができてしまうと変更できないので、課題解決は次世代へ持ち越しとなりかねません。その点、今回はプロトタイプの段階からしっかり議論ができました。画素単独の設計だけでは実現できなかった新しい価値の提供や根本的な課題解決を、いま開発している機種で行うことができました。
画素は、製造で性能が決まる部分も多いので、できるだけ工場へ行ったり現場の担当者と会話をしたりして、製造現場で情報をくみ上げるように心がけています。特性に何らかの問題が出た際に、設計したレシピ通りに作っていないからなのか、あるいは装置にトラブルがあったからなのか、それを、工場の人たちと粘り強く探っていくのも、私たち画素設計の重要な役割なんです。
イメージングとセンシング
──イメージセンサーは、スマートフォンのカメラに使われることが多いと思うのですが、今後は、どういうところで活用されていくとお考えですか?
中溝:例えばファクトリーオートメーション(以下、FA)などの工場向けや、セキュリティ、あるいは車載用カメラとか、いろいろなところに広がっていくと思いますし、期待しています。その一方で、スマートフォンも、例えば多眼化のトレンドが広がったりしていますので、拡大の余地はあると思っています。
さまざまな用途のカメラに、イメージングだけでなくセンシングの機能を取り込む流れが広がっています。FAやセキュリティの領域では、これまで追求してきた「人が見てキレイだと思う画質」とは異なる価値が必要になります。例えば工場ではフレームレートを上げて、「高速で動いている被写体をブレずに撮像できる」ことが大切です。この場合、人が見てキレイである必要はありません。あるいは、距離を測ったり、ラベルを認証したり、不審者を監視したりするためには、画質の精細さよりも被写体を検知できるかどうかが重要になってくるわけです。
目的がセンシングになった時、「どういうセンサーの特性が、その目的に対して一番ふさわしいのか」ということを、考えていかなければなりません。センシング用途のイメージセンサーの可能性に、ほかのチームも含めてしっかりと対応して、新しい価値を生み出すアクションを起こそうとしています。
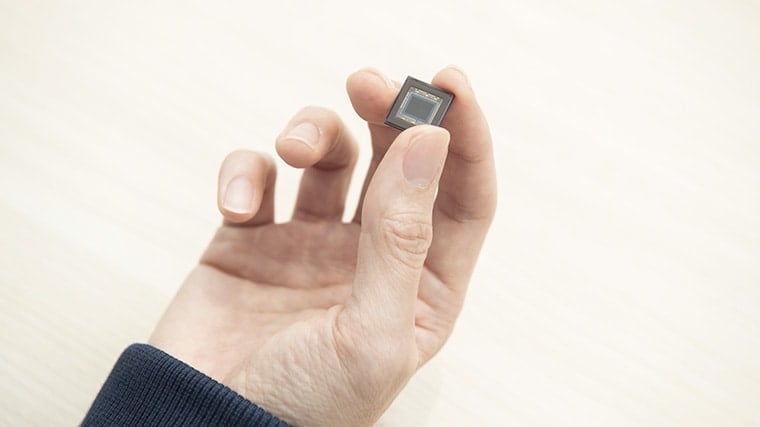
開発中に評価を行ったテスト用チップ
──では、ソニーのイメージセンサーの強みとは?
中溝:個人的にはやはり、画素性能の違いだと思います。画素は、目に見える実世界から電気的な世界への入り口です。これはイメージングでもセンシングでも変わりません。画素で光を電気信号に変えることがすべてのスタートになるので、ノイズの発生を抑えて高い感度性能を実現したり、新構造や微細化を他社に先駆けて実現することが製品の差異化につながっています。
あとは、信号処理のアルゴリズムを考える人たちが近くにいますし、イメージセンサーを製造する工場もグループ会社なので、全体最適化をやりやすいという点も強みだと思います。何か課題が出た時、どこに問題があるのかという解析もすぐに関係者が集まってできますし、何か新しいことをしようとする時も、必要な知識を持った人たちを集めやすい。新しい機能について議論をしようとなった場合も、「画素担当はあの人を呼んで、アナログはあの人、システム担当も」といったかたちですぐに必要な人が集められます。ある程度仕様が固まってきたら、製造現場の人に早いタイミングで入ってもらったり、試作後のテストについて議論したりと、迅速に開発を進めることができます。
そうやって開発のスピードを上げていくことに加えて、今後は新たな価値も提供していける集団になっていければと思います。
センシングに関していうと、お客様の側でも、どういうものがいいのかまだ手探りの部分がありますから、ある用途に対しては、「ソニーのセンサーを使ったソリューションで、お客様が考えている以上の感度や精度が出せて、こういうアプリケーションにも使えますよ」といった提案をしていくことが、センシングの新しい分野を開拓するために大事だと考えています。
もちろん、従来のイメージング領域に関しても、社内のチーム連携で、ソニーにしかできない画質の実現を狙っていきたいと思います。
画像処理アルゴリズム
付加価値をもたらすのが、画像処理の役割
──画像処理アルゴリズムとは、イメージセンサーにおいてどのような役割を担っているのでしょうか?
藤田:シンプルにいうと、その名の通り画像を処理しているわけですが(笑)、具体的には、画像自体をキレイにするとか、センサーで新たな機能を実現するといったことに取り組んでいます。
今回のIMX586でいうと、「ハイダイナミックレンジ(以下、HDR)画像の合成」や、「Quad Bayer配列」に対して高感度と高解像度を両立させるための配列変換の処理、あとは「位相差検出」という高速オートフォーカスに必要な情報を出すための処理、といったところが大きな役割です。最近は背景をボカしたポートレートモードが流行っていますが、そのソリューションを用意することなども、私たちの役割でした。
──Quad Bayer配列について、もう少し詳しく教えていただけますか?
藤田:夜景など暗いシーンを撮影する時には、隣りあう4つの同色のカラーフィルターの画素を加算し、画素サイズを1.6μm相当(有効1200万画素)にすることで感度を高め、低ノイズで明るい画像の撮影を可能にします。一方、明るいシーンの場合は、信号処理によってリアルタイムで4800万画素に配列変換し、高解像度の撮影を可能にします。それが、Quad Bayer配列です。
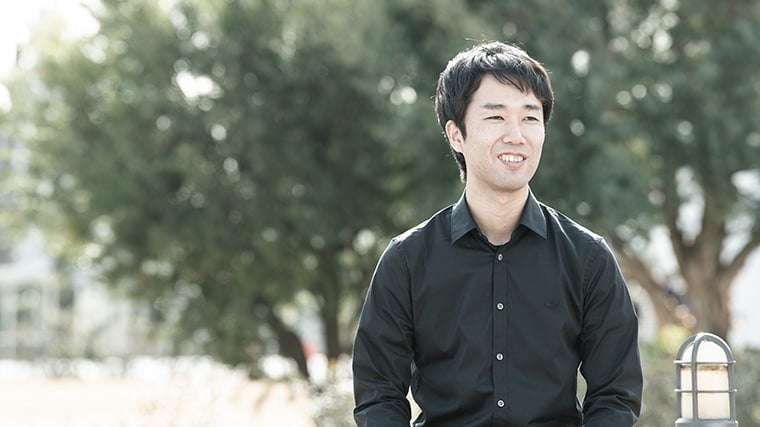
──IMX586の開発において、とりわけ難しかった部分を教えてください。
藤田:画素が小さくなると、どうしても感度が下がってしまいます。つまり、出てくる画像の質が落ちるというか、ノイズが増えてしまいます。それによって、いままでの配列変換やHDR合成や位相差検出の処理といった部分が全部影響を受けてしまいます。そこをうまく合わせ込むというか、「センサーの感度が少し悪くなっても、問題ない性能を実現する」というところが、難しかったです。
画素を微細化すると、どうしてもセンサーとしての特性が落ちるので、その部分を信号処理で補うことが私たちの役割だといえます。
また、昨今のスマートフォンのカメラは高速オートフォーカス機能が当たり前になっているため、どんな配列変換をしようが、広いダイナミックレンジで撮ろうが、ユーザーには「オートフォーカスしたい」という欲求があると思います。実は特性を補いながら高速オートフォーカスを実現する「配列変換と位相差検出」、または「HDR合成と位相差検出」を同時に行うことは非常に難しく、信号処理だけでは解決できない部分もありました。画素からデータを読み出す時の駆動方法を工夫しなければいけなかったわけですが、画素やほかの部分の設計者が協力しあい、全体最適化を行ったことで、最終的にはブレイクスルーを実現できました。
スマートフォン向けセンサーも
まだまだ改良の余地がある
──IMX586の開発に一区切りがついたいま、藤田さんはどのような領域の研究開発に関心を持っているのでしょうか?
藤田:ここ5〜6年で、イメージセンサーの下に信号処理のチップを合わせて積層してしまう、という技術が広く普及しました。
スマートフォン用のイメージセンサーの場合、小型化するためにどうしても面積的な制限が伴います。限られた面積に、できるだけ多くの機能を搭載する、という点が、一番難しくもあり重要なところだと思って開発を続けています。その背景には、性能の良い一眼カメラのキレイな画像と遜色がない画像を実現することで、スマートフォンのカメラを使うユーザーの体験を高めたいという思いがあります。
──スマートフォン用のイメージセンサーには、この先どのような可能性があり、それに向けてどのような準備をしているのでしょうか?
藤田:さらなる微細化に向けた準備もしていますし、センサーを使って画像を撮影する以外のいろいろな機能を実現できるように研究を続けています。例えば、被写体までの距離を測定できるようにすることで、イメージング以外の体験ができるようにしようとしています。まだ開発途上のため、詳しくはお話できませんが、アイデアレベルでいうと、例えば物体の表面状態や、立体的な形状を測るといったことはできると思います。
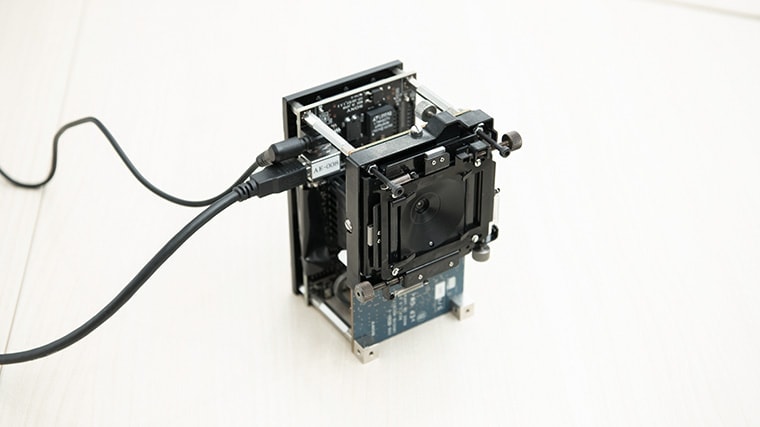
イメージセンサーを評価する環境
──スマートフォン向けのイメージセンサーが、今後解決していかなければならない課題と、スマートフォン以外に可能性を感じている分野を挙げるとすると?
藤田:課題はスマートフォンの薄さを保ちながら性能を補うことです。薄さを保つにはイメージセンサーもレンズも小さいものしか搭載できません。今回、小さなレンズの性能を補うために、配列をうまく変換して、光学ズームと比べて遜色のない電子ズームを実現することがある程度できたのですが、さらなる性能向上を今後も目指していく必要があると思います。
スマートフォン以外の分野としては、車載とか監視とか、イメージセンサーの出番はいろいろあると思いますし、社会の中でイメージセンサーがあらゆる場所で使われていくという流れは、おそらく止まらないと思います。スマートフォン向けのイメージセンサーで培った技術をほかの分野と融合して、さまざまな価値提供ができるようにしたいと思っています。
──藤田さんは今後、どのようなキャリアを描いていますか?
藤田:これからは、センシングの方向性も広がっていくわけですが、イメージングはイメージングで、画素やデバイスの特性を知っていないと開発が難しい部分があると思います。ですので、画素もデバイスも信号処理もわかれば、できることがますます広がる。元々、大学の専攻がデバイス設計に近かったため、デバイス設計にも興味があるんです。複数の領域を横断的に理解できる人材は貴重になっていくと思います。
例えば、「イメージセンサーとして、この特性を実現するには、この部分はあきらめざるを得ない。ならば、できない部分は信号処理でなんとかする」という割り切り方を知っていることで、センサーシステム全体として、最適なソリューションを導き出せるようになりたいです。
デバイス
人材育成と技術開発を両立する難しさ
──ソニーの半導体の設計・開発・製造における、ソニーセミコンダクタマニュファクチャリング株式会社の役割について教えてください。
渡辺:私たちソニーセミコンダクタマニュファクチャリング株式会社(以下、ソニーセミコンダクタマニュファクチャリング)が主体となってデバイス開発するケースと、ソニーセミコンダクタソリューションズ株式会社のデバイス開発部署と協力しながら開発する、二つのケースがあります。ソニーセミコンダクタマニュファクチャリングは、プロセスの構築と試作を行って、特性、品質の向上を図る開発と、その後の量産を主な役割として担っています。
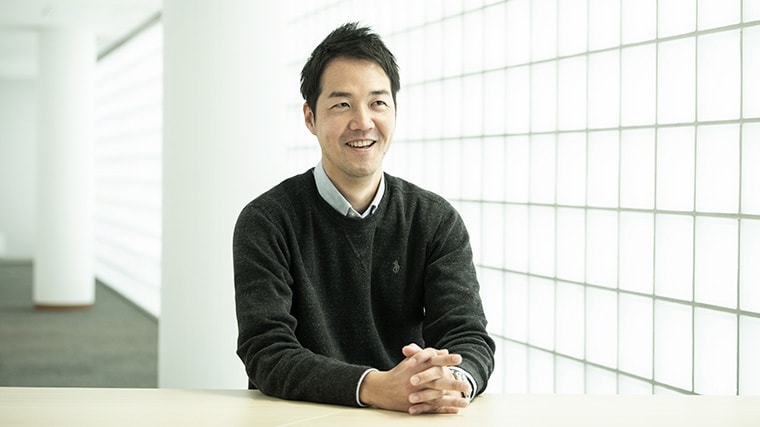
──今回、渡辺さんはどのような役割を果たしたのでしょうか?
渡辺:私は長崎テクノロジーセンターに入社以来、カムコーダーや監視、デジタル一眼用大判、スマートフォン用などのイメージセンサーの開発を担当してきましたが、大分テクノロジーセンターがソニーセミコンダクタマニュファクチャリングの仲間入りをした2016年に、立ち上げメンバーとして大分に異動しました。
ソニーセミコンダクタマニュファクチャリングに新たに加わった大分テクノロジーセンターのメンバーと一緒に、イメージセンサーを開発、量産するにあたって、どのような流れで開発を進めていくのか、開発するうえでキーとなるポイントやノウハウの共有などを伝えていくという役割も担いながら、0.8μm微細画素の開発にチャレンジしました。
──新規立ち上げに際して、どのような苦労があったのでしょうか?
渡辺:一つ目はスケジュールの管理です。IMX586の画素サイズは世界初の0.8μm微細画素という新しいテクノロジーになるので、当初はスマートフォン用イメージセンサー開発の基幹製造事業所である長崎で基礎開発が進んでいたのですが、そのほかの製品開発、リソースや量産などの都合で、大分で開発と量産を行うことになりました。
大分はほかのテクノロジーセンターと比べるとイメージセンサー開発の経験、実績が少なく、難しいテクノロジーを使った製品開発の先頭に立つことになるとは考えていなかったため正直驚きました(笑)。
二つ目はチームの統制をとることです。大分テクノロジーセンターは、ソニーセミコンダクタマニュファクチャリングに加わってから日が浅かったこともあり、開発の進め方や、文化が大きく異なりました。そのため、大分工場の文化とソニーセミコンダクタマニュファクチャリングの文化をスムーズに融合していくというのが、私のミッションでもありました。このIMX586の開発はスケジュールが非常にタイトだったこともあり、それを達成しつつ、チームを一つにしていくという部分に、大きな苦労がありました。
──イメージセンサーの進化を、渡辺さんなりに振り返っていただけますか?
渡辺:私が入社した2003年当時は、CCDからCMOSイメージセンサーへの転換期でした。画素サイズが2μmと大きく、ハイビジョンに対応したイメージセンサーが登場し始めたころでした。そのころに比べると、スマートフォン用イメージセンサーの性能は飛躍的に向上し、多画素化によりコンパクトデジタルスチルカメラや、カムコーダーの役割を担えるほど十分な画像を撮ることができるようになりました。また一方で、微細化も大きく進んでいる、という印象です。
多画素化と微細化の過程において、ソニーでは裏面照射型構造という技術的なブレイクスルーがありました。従来は、受光面の上に配線層を配置し、上から集光する構造だったのですが、受光面を一番上にして配線が邪魔にならない構造にすることで、大幅に感度を向上させることができました。この技術によって、微細な画素サイズでも高感度の撮影が実現できるようになったのです。

画素深部制御への挑戦
──先程、新規メンバーを育てながら短期間で開発する苦労についてお聞きしましたが、IMX586の製造では、どのような苦労があったのでしょうか?
渡辺:イメージセンサーを製造するプロセスの一つに、フォトリソグラフィーという工程があります。単純にいうと加工する場所しない場所、不純物を注入する場所しない場所を区分けする工程で、イメージセンサーを作り上げるために最も重要な工程なのですが、画素の微細化が進むと、シリコン基板の深さ方向にフォトダイオードを作っていくことになります。そのためには、高いエネルギーでシリコンに不純物を注入しなければなりません。
また、このフォトリソグラフィー工程では「厚膜(あつまく)レジスト」というものを使うのですが、その厚膜レジストの形状変化による撮像特性の変動に、今回はとりわけ苦労させられました。同じ装置での加工再現性、ウェーハ面内の均一性を向上させる点に沢山の時間を費やしました。
──神奈川・厚木の開発メンバーとはどのような役割分担があったのでしょうか?
渡辺:まずは画素形成の肝となるフォトリソグラフィー工程のパターニングが画素設計通りに行われているか、という条件確認を、プロセスエンジニアと相談しながらやっていくところから始めました。
その後は、試作を行い、その結果を評価し完成度を高めていきます。評価は撮像特性の観点では画素設計者が、デバイス特性は厚木のデバイス担当者が、特性とプロセス管理の見極めは大分のデバイス担当者が行い、協力しながら要求特性を満たし、かつ最も高い歩留まりが得られるプロセスウインドウの見極めに集中して取り組みました。
今回はそれぞれの機能をうまく分担し協力できたことが開発のスピードを上げられた一つの要因だと思います。
──イメージセンサー開発の面白さと、製造プロセスにおける課題とは何ですか?
渡辺:ソニーのいいところなんですが、開発に自分の意見が反映できるんです。ソニーセミコンダクタマニュファクチャリングは、ソニーの自社工場という位置づけなので、ソニーの設計通りに淡々と製造するだけなのだろうと入社当時は思っていたのですが、デバイス開発という分野においても厚木の開発メンバーと同じ目線で話ができるので、そこにやりがいを感じています。
初めて担当したイメージセンサーを搭載したビデオカメラが世の中に出て、「画像がキレイ」と知人に言ってもらえた時は、感動しました。そういった反応が得られることが、ものづくりの醍醐味だと思います。
製造プロセスにおける課題は、バラつきを抑え、高い歩留まりを維持することです。臨機応変に需要に対応するために複数の工場で量産を行うことがありますので、工場間の撮像特性のバラつきを抑えることが必要です。また、装置の個体差、材料の違いによって生じる特性差、歩留まりの低下などの問題を解消することも大きな課題で醍醐味でもあります。