Collaboration
ものづくりのプロ集団としての"誇り"と"責任"で社会に貢献を~ 人工呼吸器生産支援 担当者インタビュー
2020年10月27日
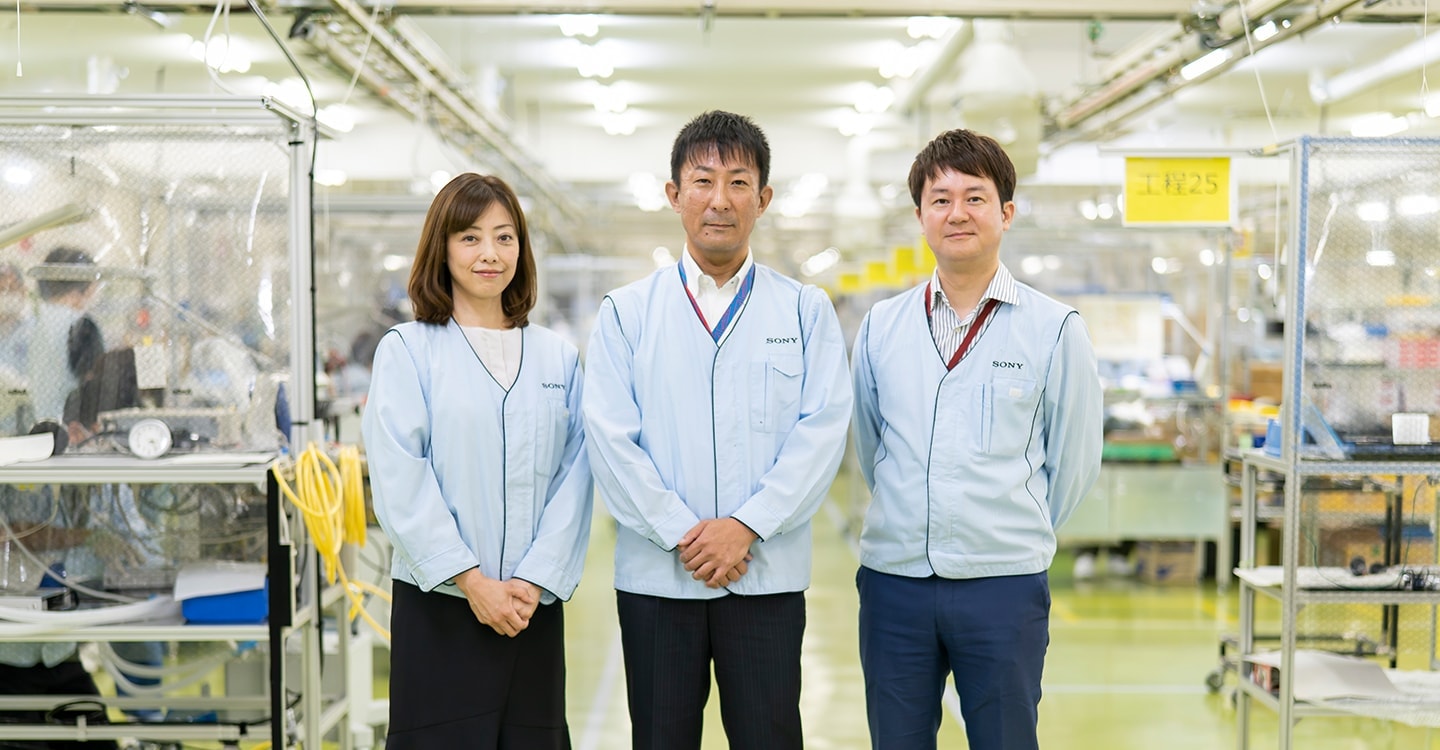
新型コロナウイルスの感染拡大により、治療のための人工呼吸器の不足が懸念される中、ソニー株式会社(以下、ソニー)は社会貢献の一環として、日本政府(経済産業省・厚生労働省)からの「人工呼吸器の生産支援」要請に協力していく意思を表明しました(2020年5月)。
ものづくりのプロフェッショナル集団として、これを担ったのがソニーグローバルマニュファクチャリング&オペレーションズ株式会社(以下、SGMO)です。長年のエレクトロニクス製品で培った経験・スキルを活かし、アコマ医科工業(株)(以下、アコマ)とタッグを組んで、わずか2ヵ月で500台という大量生産に挑戦しました。
SGMO、そしてソニー初となる、人工呼吸器の生産、またアコマとの協業について、プロジェクト責任者の浅島 史郎、製造技術および顧客担当の玉村 和之、QMS担当の中島 利佳に話を訊きました。
プロフィール
-
浅島 史郎
ソニーグローバルマニュファクチャリング&オペレーションズ株式会社
クライアントリレーション部門
副部門長 -
玉村 和之
ソニーグローバルマニュファクチャリング&オペレーションズ株式会社
メディカルセンター
メディカル1部 -
中島 利佳
ソニーグローバルマニュファクチャリング&オペレーションズ株式会社
メディカルセンター
メディカル品証部
──はじめに、経歴について簡単に教えてください。
浅島:もともとテレビ事業部で、海外赴任も含め計23年の間、パネルとメカの設計を担当しました。その後、単一の商品カテゴリーやメカという領域にとらわれず、もっと幅広いことに挑戦したいと考え、2015年に今の組織の元となる新規事業を主体とした組織を作り、現在5年目となります。その一環で今回の人工呼吸器の製造支援にも携わることになりました。
中島:私は愛知県・稲沢サイトでグローバル化を推進するプロジェクト業務に従事していました。そのプロジェクトが終了した後、愛知県・幸田サイトに医療機器の製造を導入することになり、民生機器とは異なる医療機器独自の考え方・文化を根付かせるため、2014年から教育体系の整備やQMS(品質マネジメントシステム)構築、及び維持管理業務を担当しています。
玉村:私は中途採用で、以前は自動車のパーツを設計していましたが、最終完成品を手がけたいという想いで、SGMO(当時のソニーEMCS)に転職。サイバーショット、ハンディカムの商品設計を経て、2015年から医療機器の製造技術を担当しています。
政府の要請でソニーが支援を表明
──今回、人工呼吸器の生産支援を行うことになった背景について教えてください。
浅島:日本で新型コロナウイルスがはやり始めた今年の3月頃、医療現場で人工呼吸器が足らないというニュースがよく報道されていたと思います。実のところ、日本に流通する人工呼吸器はほぼすべて海外からの輸入に依存しており、世界中で人工呼吸器が逼迫している状況下では輸入もままならない状態でした。
そこで人工呼吸器の国内増産を図るべく、日本政府(経済産業省・厚生労働省)の主催で医療機器メーカーと他産業の製造メーカーによるマッチングイベントが行われ、そこにソニーも参加したのです。いくつかの医療機器メーカーとお話をする中で、最終的にアコマが必要としているサポートと、SGMOが貢献できることがマッチしたため協業が実現しました。
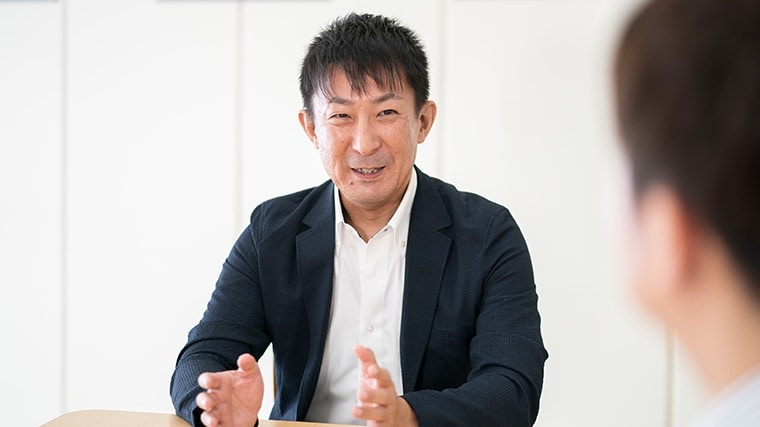
医療機器を手がけているソニーへの信頼と安心
──SGMOへの生産受託は、何が決め手になったのでしょうか。
浅島:ポイントは大きく3つあります。一つは、「社外ビジネスの経験があること」。実は今回、皆さんが最も驚いていたのは「ソニーは他社製品も作れる」ということ。ソニーの会社だからソニー製品以外作るはずがないと思われていたようで、生産のみならず、設計や部品調達などのスキームがすでに整っており、多数の実績があることは意外だったようです。
2つめは「現在も医療機器を生産しており、ISO13485を認証取得していること」。特に、医療機器産業に特化した品質マネジメントシステムの国際規格であるISO13485の認証を取得していることは、安全で品質の高い医療機器を提供できると認めていただくポイントとなり、大きなアドバンテージでした。
そして3つめは、「大量生産が可能であること」です。アコマの人工呼吸器ビジネスは少量生産が中心であり、その規模は1年で100台ほど。政府からの要請である「2ヵ月で500台」という数に対応するには、我々の力が不可欠と判断いただきました。今回いくつかの大手企業が手を挙げる中、ここまで全面的に対応できたのはソニーだけだったと思います。
"部品がない!"からのスタート
──生産支援を通じたアコマとの協業において、どんな苦労がありましたか?
玉村:会社が違うので当然ですが、すべてにおいてやり方が異なります。例えば部品は、ソニー内であれば同じ部品番号、同じシステムで連携してやりとりできますが、アコマの部品番号はアコマ独自のもので、すべてマニュアル管理になります。
また、それ以上に苦労したのは、今回増産対応した機種はアコマが20年前に設計し、10年前に生産終了しているもの。それゆえ世の中に流通していない部品もあり、市場在庫品を探すところから始まりました。
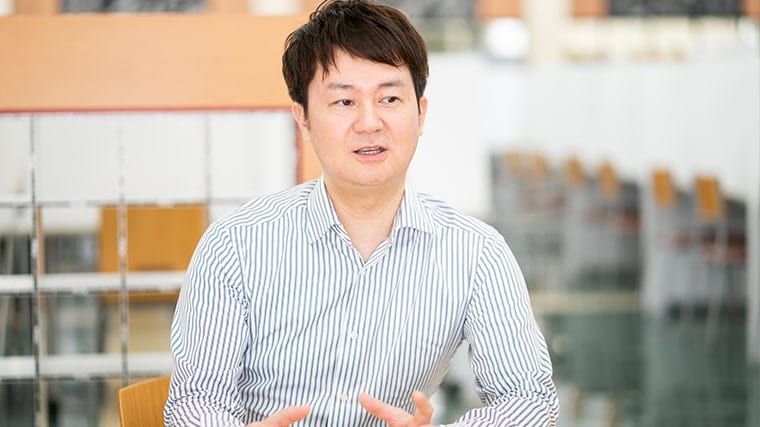
"職人の手感"をすべて定量化し、量産体制を構築
玉村:生産においては、20年前の設計ということもあり、部品の締め付けトルクなどが数値で記載されておらず、作る人の感覚に任されていました。
今回それらをすべて定量化し、規格を定めました。最初は良い”塩梅”の見極めが難しく、試行錯誤する中で締めすぎて壊してしまうこともありました。
浅島:これまでのアコマでの生産は1日1台程度の生産だったからこそ、熟練された職人のノウハウとスキルがあればできたことも、一気に500台作るとなると、誰がやっても同じ品質となるための手順を準備することが重要です。
玉村:それらを作業手順書に書き起こすのと並行して、2ヵ月で500台、つまり1日あたり15台生産できるようタクトタイムを算出し工程設計を行いました。こういったところは我々の得意領域であり、アコマから最も期待されていたことでもあります。
一方、人工呼吸器というのは、空気と酸素をブレンドして患者の体内に送り込んでいるわけですが、それらの流量やタイミングなどはアコマ独自の設計ノウハウとして製品に落とし込まれており大変勉強になりました。
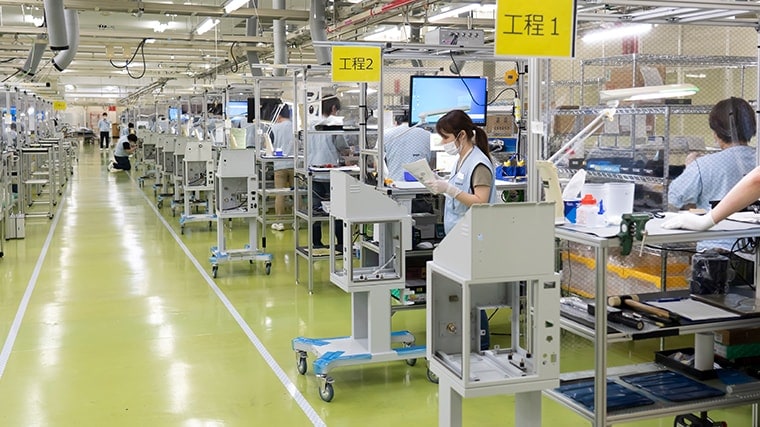
一日15台を生産すべく分業化された生産ライン
前例のないクラスⅢ(高度管理医療機器)の壁
中島:医療機器は各国法規制に基づき、人体へのリスクの大きさに応じてクラス分類されており、日本の薬機法(医薬品、医療機器等の品質、有効性及び安全性の確保等に関する法律)のもと、クラスⅠ(最もリスクが低い)からクラスⅣ(最もリスクが高い)までの4分類があり、今回の人工呼吸器は「クラスⅢ」に相当します。ソニーで生産する医療機器は、アメリカにおいて「クラスⅡ」に分類されるものもありますが、国内においては「クラスⅠ」(一般医療機器)の経験しかなかったため、生産受託が決まったときの第一声は「いきなりクラスⅢですか?」でした。クラスⅢは「高度管理医療機器」になるため一気にハードルが上がります。中期的には高いクラスへのチャレンジも予定していましたが、突然かつ、経験のないクラスⅢという高い壁に、どうやって対応していこうかと頭を抱えました。
通常、製造業者(製品の製造のみを担う)と製造販売業者(製品の最終責任を負う)は一体となって医療機器を市場に出すため、SGMOのQMSは、製造販売業者であるソニーの事業会社のQMSとのつながりをもたせて構築しています。
しかし今回は、アコマの仕様で動くことがベースになるので、すり合わせに時間がかかりました。製品実現領域においては部品や作業標準書などはアコマから提供していただくのですが、製品実現に関わる周辺プロセスに対する要求は自社ルールとは異なるものだったため、自社ルールにどう当てはめるか、矛盾がないよう短期間でどこまで対応するか悩みました。
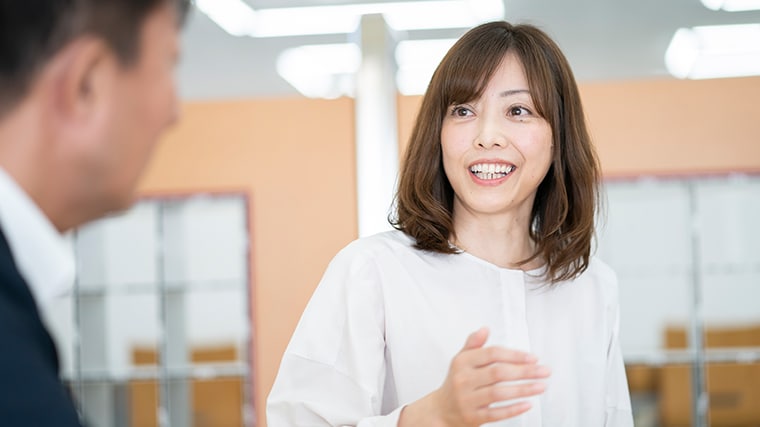
浅島:対応に苦心したという点では、今回途中で方針変更があり、急遽幸田サイトで「製造業」を取得することになりましたね。
日本では薬機法により、本来、医療機器の製造を行う場合、製造所は厚生労働大臣の登録を受けなければいけませんが、当初は生産支援という立場から、アコマより製造業登録不要として本プロジェクトをスタートしました。しかし、打ち合わせを重ねていく中で、生産のかなりの部分をSGMOが担当するため、「主たる組立て」に相当するとアコマが判断し、顧客要求に応える形で申請を行いました。
中島:手続き自体はそれほど大変なことではありませんが、迅速に対応すべく、手続きのための申請資料作成など担当者が汗だくになって登録に走りました。また登録することで求められる責任も大きくなります。クラスⅢでは厚生労働省所管のPMDA(独立行政法人医薬品医療機器総合機構:Pharmaceuticals and Medical Devices Agency)による適合性調査があり、大変厳しい調査と聞いています。それが冒頭の「いきなりクラスⅢですか?」という言葉につながるわけです。
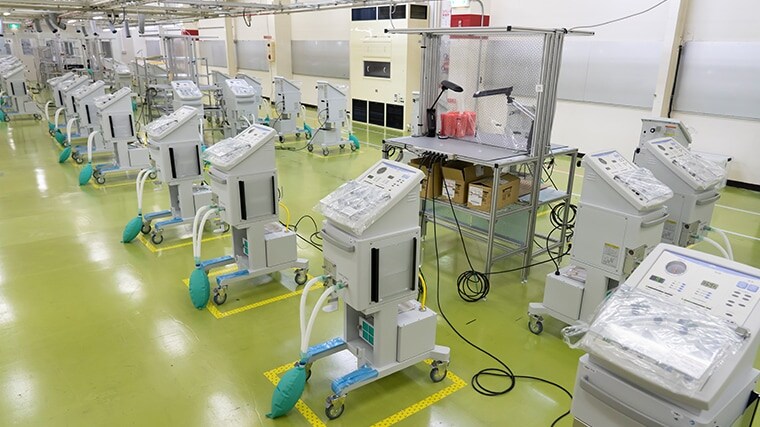
約30時間かけて全数をエージング検査
──アコマとの協業で、どんな気づきや学びがありましたか?
玉村:やはり他社を知ることができたのはとても良い経験でした。例えばクラスⅢに対応したものづくりはどうあるべきかと考えたとき、我々なら構えてしまい、過剰に厳しいルールを設けてしまうと思います。やればやるだけコストもかかるため、この領域への新規参入は難しいと懸念していましたが、アコマとの協業を通じて、リスクが高いところは厳格に管理し、そうでないところは思い切った割り切りをするなど、きちんと層別管理をすることでコストをかけずに体制・仕組みをつくるためのヒントを得ることができました。
浅島:今までソニーがやってきた「標準」が必ずしもすべてに当てはまるわけではない、というのは大きな気づきでしたね。医療分野ということで、ソニーの医療機器のものづくり領域を担う組織、メディカルセンターのノウハウが役に立つと考えていましたが、良くも悪くもかなりの部分で独自の考え方や違いがありました。そういう意味で、アコマの例が次も当てはまるとは限らないため、毎回相手から「学ばせていただく」という姿勢で臨みたいと思います。
玉村:アコマの皆さんからは、定量化やSGMOの工程設計が勉強になったと言っていただきました。量産期間中は出来栄え確認や判断をしてもらうためにアコマのメンバーが常駐していたのですが、アコマとしてもソニーのものづくりを勉強したいという想いで、意識的に若手メンバーを派遣していたとのことです。今回の協業はお互いにメリットがあり、アコマの工場長からは「またぜひ協業したい」とポジティブな言葉をいただいています。
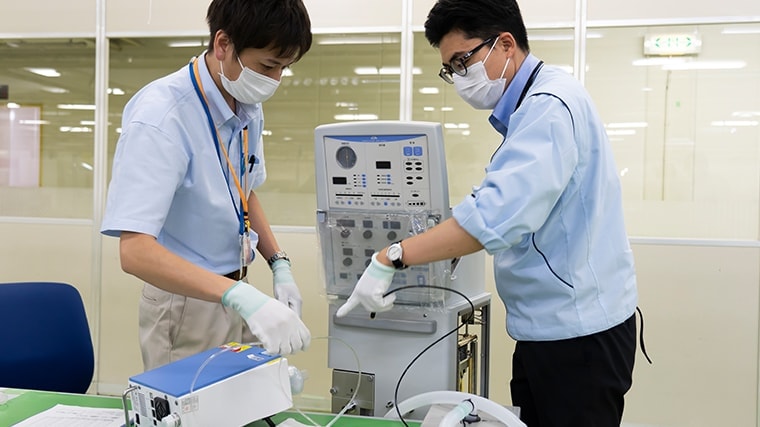
アコマのメンバーとともに動作を確認
世の中の役に立つもので"感動"を
──最後に、人工呼吸器生産を通じて、改めてものづくりに対する想いを聞かせください。
中島:医療は社会基盤において必要不可欠であり、その側面を担えることに誇りを感じています。QMSとして、ソニーだけでなく社外の医療機器においても安定した品質の製品を供給するための仕組みを担っていくことを自分の使命とし、医師、患者さんを支える存在でありたいと思っています。
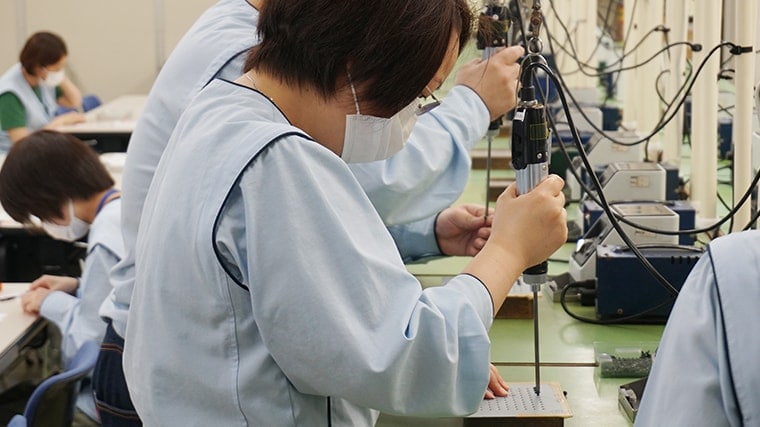
安定した製品を作るための作業訓練の様子
玉村:最初にお話した通り、最終完成品を手がけたいという想いでこの会社に入社し、デジカメやビデオカメラの商品設計を通じて「人に感動を提供する喜び」を味わうことができました。次は「人の役に立つことをしたい」と考えていたとき、ちょうどSGMOが医療機器のビジネスを拡大していくタイミングで、ぜひやりたいと立候補しました。というのも、学生の時に友人を癌で亡くしており、こんなに若くても生きられない人がいるということがショックで、「いつか医療に携わってみたい」という気持ちがずっとありました。思いがけずこの会社でチャンスに恵まれ、そして今世の中で必要とされている人工呼吸器に携わることができ、とてもやりがいを感じました。ソニーは”感動”を創り出す会社ですが、その感動は「生きていく上でなくてはならないもの」「医療従事者の方が楽になるもの」を形にすることでも実現できると思っています。ソニーならではのクリエイティビティとテクノロジーで、社会に貢献していくことが技術者としての私の目標です。
浅島:我々はものづくりのプロ集団として常に新しいことにチャレンジしていきたいと思っています。今回は政府からの要請が大きな後押しになりましたが、例えばクラスⅢの対応も、最初は無理だと思っていたことも、やってみたらできたという経験は大きな自信になったと思います。新しいことや難易度の高いことをやり始めるとき、「どうしよう」と二の足を踏んでいるときは、恐れず、一歩前へ進んでみることが重要だと思います。
また、人工呼吸器の流通状況についてお話をうかがったとき、医療機器もコストを理由に多くが海外生産になっていることをつくづく感じました。人の命にかかわるものなど、「日本でやらなければならないもの」が実はたくさんあるんじゃないかと思ったため、今回のような不測の事態に、ソニーのような会社がすぐに対応できる体制を準備しておくことは大変有意義だと実感しました。すぐに利益にはつながらなくとも、今後も何らかの形で社会に貢献していけたらと考えています。
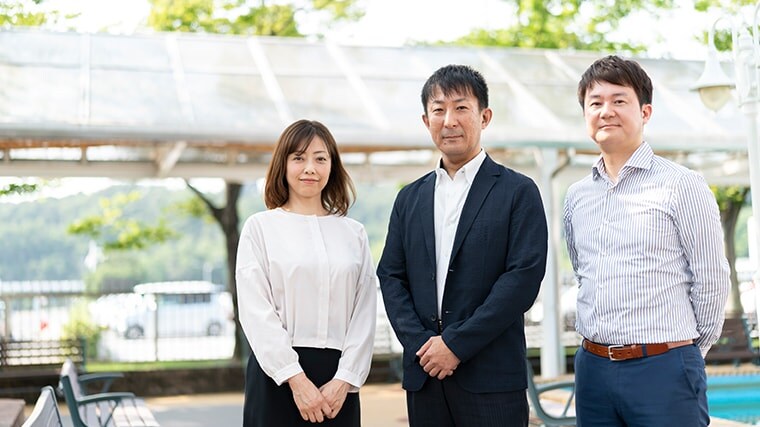
■アコマ医科工業株式会社
1921年の創業以来、麻酔器・人工呼吸器を中心とした医療機器の製造・販売を行う企業。日本で初めてのアネロイド型血圧計や独自開発した麻酔器と人工呼吸器の機能を持つ「アネスピレータ」など、医療の現場へ先進機能を搭載した革新的な製品をお届けしています。
アコマ医科工業(株)ホームページ:https://www.acoma.com//